—
future of industry
L’importanza del restare al passo con la crescita della produzione di batterie attraverso lo smart measurement
Il mercato in rapida crescita dei prodotti elettronici e di alimentazione, dai dispositivi portatili ai veicoli elettrici e ai sistemi di accumulo di energia, ha visto una massiccia espansione nella produzione di batterie, mentre le aziende devono potenziare la loro capacità di tenere il passo con la domanda. In questo articolo, Diana Garcia di ABB Measurement & Analytics evidenzia il contributo essenziale della tecnologia di misurazione intelligente nell'aiutare i produttori di batterie a mettere finemente a punto i loro processi di produzione per prestazioni ottimali.
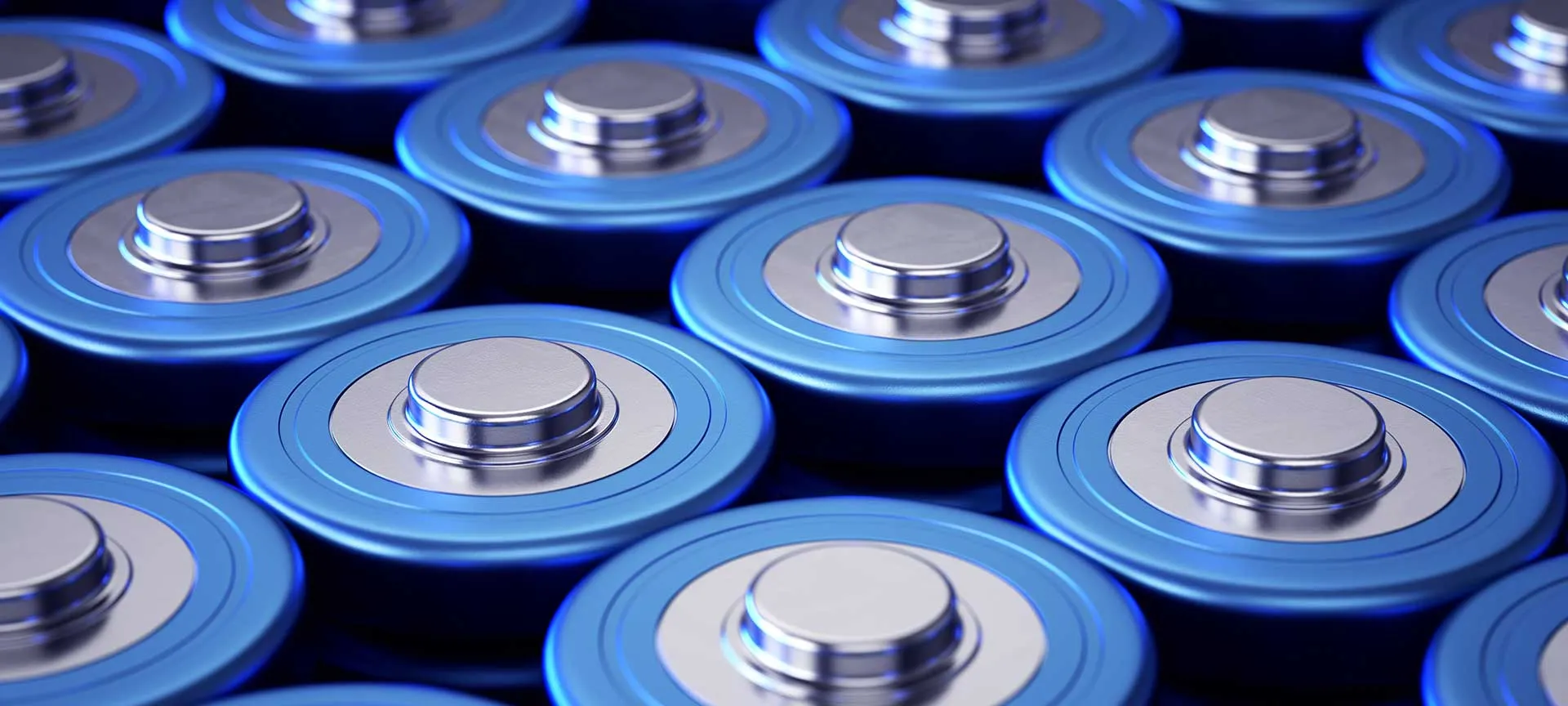
La capacità produttiva dovrebbe aumentare vertiginosamente
La capacità della produzione di batterie agli ioni di litio dovrebbe assistere ad una un'ulteriore crescita nel prossimo futuro. Le proiezioni attuali suggeriscono che potrebbe raddoppiare entro il 2025, trainata principalmente dall'aumento della domanda di batterie nei veicoli elettrici e nei sistemi di accumulo di energia rinnovabile. Le principali sfide verso l’aumento della produzione includono la disponibilità limitata di materie prime e le preoccupazioni etico-ambientali per le pratiche di approvvigionamento, il riciclaggio delle batterie e lo smaltimento delle batterie, una volta a fine vita. Tuttavia, le parti interessate sono ottimiste sul fatto che nuovi sforzi di ricerca e innovazioni contribuiranno a sbloccare un ulteriore potenziale nella tecnologia delle batterie, portando a un futuro sostenibile alimentato da energia verde.
Le sfide nella produzione di batterie
Tra le sfide poste dalla produzione di batterie agli ioni di litio c'è l'approvvigionamento e la lavorazione delle materie prime. L'aumento della domanda di ingredienti critici per batterie agli ioni di litio, cobalto, nichel e litio può portare a colli di bottiglia nella catena di approvvigionamento. Anche le preoccupazioni etiche relative al lavoro minorile e ai danni ambientali sono emerse come potenziali ostacoli all'approvvigionamento sostenibile.
L'elevato costo degli impianti di produzione su larga scala richiede notevoli spese in conto capitale prima di poter ottenere rendimenti significativi. Un'altra sfida è trovare metodi di riciclaggio adeguati per evitare danni ambientali, mantenendo la redditività. Per affrontare con successo queste difficoltà, i produttori devono stabilire catene di approvvigionamento affidabili perseguendo al contempo pratiche commerciali etiche e rispettose dell'ambiente che garantiscano l'efficienza durante tutto il ciclo di vita della produzione delle batterie, dall'approvvigionamento, alla produzione fino allo smaltimento o al riciclaggio.
—
L'elevato costo degli impianti di produzione su larga scala richiede notevoli spese in conto capitale prima di poter ottenere rendimenti significativi.
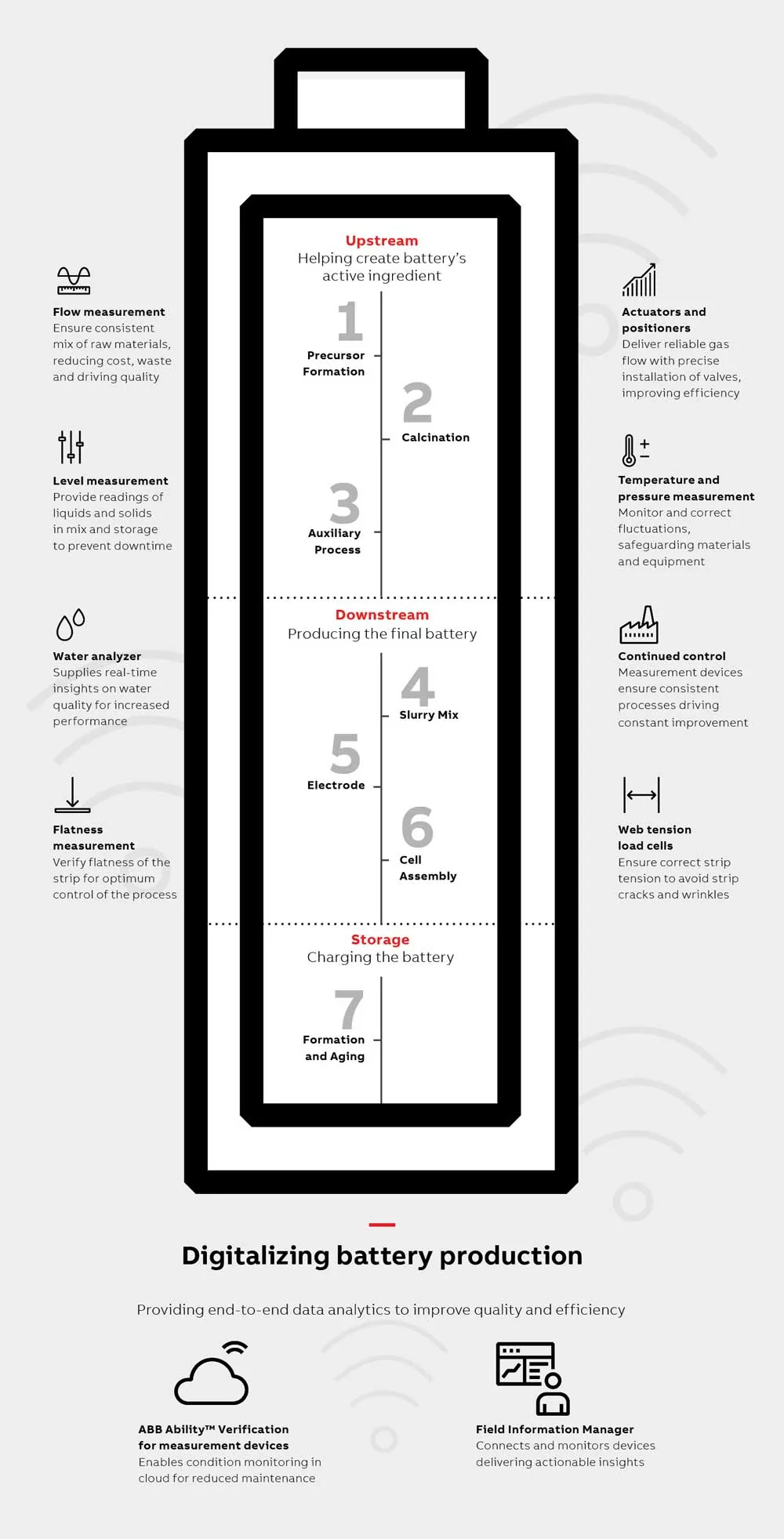
—
Un'altra sfida è trovare metodi di riciclaggio adeguati per evitare danni ambientali, mantenendo la redditività.
Punti di maggiore attenzione nella produzione di batterie
In risposta a questa domanda, diversi paesi hanno istituito centri di produzione di batterie. Questi in genere dispongono di impianti di produzione all'avanguardia con processi automatizzati avanzati. I principali attori come Cina, Corea del Sud, Giappone e Stati Uniti stanno aprendo la strada, ma paesi europei come Germania e Francia stanno intanto aumentando la produzione. Questi punti caldi svolgeranno un ruolo importante nel soddisfare la domanda di soluzioni energetiche più pulite ed efficienti in diversi settori. La transizione verso l'energia pulita e rinnovabile ha anche influenzato i governi nel dare priorità alla produzione di batterie agli ioni di litio come mezzo per immagazzinare fonti di energia rinnovabile intermittente come l'energia eolica o solare. Inoltre, i governi stanno anche investendo in ricerca e sviluppo per migliorarne l'efficienza, la sicurezza e la longevità. La Germania ha specificamente adottato misure per diventare un leader globale nella produzione di batterie agli ioni di litio sostenendo iniziative di ricerca e stabilendo partnership strategiche con i leader del settore per produrre batterie di alta qualità a un prezzo competitivo.
Un complesso processo produttivo
La produzione di batterie agli ioni di litio è un processo complesso. La prima fase prevede la preparazione dei materiali anodici e catodici. L'anodo è tipicamente costituito da grafite mentre il catodo è costituito da una combinazione di ossido di litio cobalto, ossido di litio manganese o ferro litio fosfato. Una volta che questi materiali siano stati lavorati, vengono usati per rivestire un substrato costituito da una pellicola di alluminio per formare elettrodi. Questi elettrodi vengono poi arrotolati in celle separate e posti in un alloggiamento della batteria insieme a una soluzione elettrolitica, tipicamente costituita da sale di litio sciolto in solventi organici. Ogni cella è sigillata con un separatore a membrana per evitare cortocircuiti ed esplosioni. L'intero processo richiede un rigoroso controllo di qualità per garantire che le batterie soddisfino gli standard di sicurezza e funzionino in modo ottimale per tutto il loro ciclo di vita.
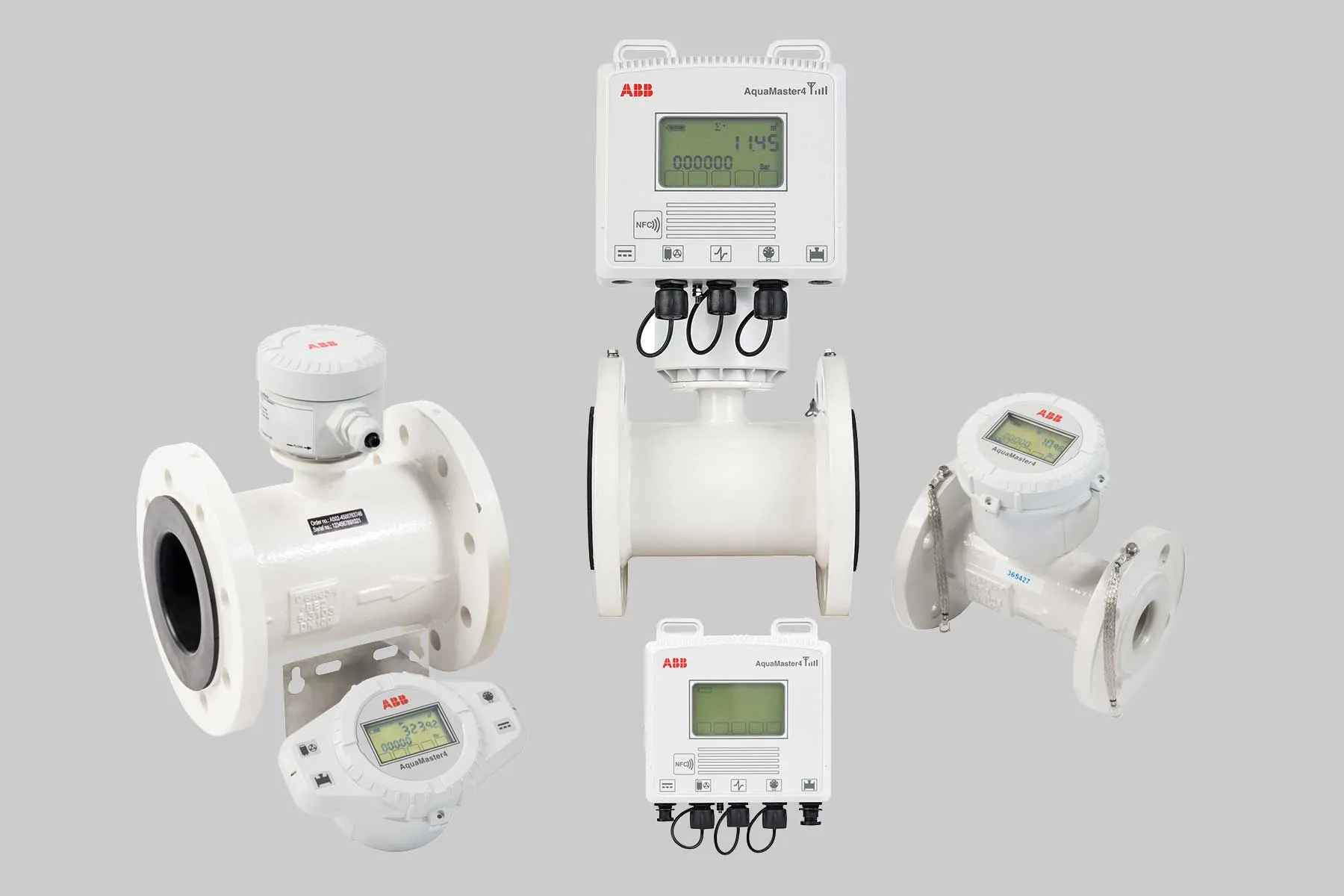
Le efficienze dello Smart Measurement
Sebbene i vantaggi delle batterie agli ioni di litio sono molti, la tecnologia Smart Measurement promette di razionalizzare ulteriormente questo processo riducendone i costi e tempi. Utilizzando sensori e analisi dei dati, i produttori possono monitorare e misurare ogni fase del processo di produzione. Ciò consente loro di identificare tempestivamente potenziali problemi e apportare le modifiche necessarie per garantire prestazioni ottimali e longevità delle batterie.
Strumentazione, analizzatori, misurazione della forza e soluzioni digitali sono componenti essenziali per migliorare l'efficienza e la qualità.
In ogni fase, parametri come pressione e temperatura devono essere misurati con precisione per garantire la produzione secondo le specifiche. La prima fase è la produzione degli elettrodi. In questo processo, viene miscelata una sospensione di materiali attivi, leganti e additivi. La misurazione della temperatura è importante qui poiché la miscelazione dell’emulsione (slurry) viene condotta tra i 20 e 40°C.
L'emulsione viene quindi usata per rivestire entrambi i lati dei collettori di corrente. È richiesta un'elevata precisione poiché la fase di rivestimento richiede la misurazione dello spessore del film secco con una precisione di +/- 2 g/m2. La fase di rivestimento prevede che l'emulsione venga distribuita su due strati di lamina metallica in alluminio per il catodo e rame per l'anodo, rivestendoli. I nastri vengono quindi spostati costantemente attraverso una sezione di essiccazione per rimuovere il solvente. Le velocità delle lamine durante l'asciugatura devono essere mantenute tra 35m/min e 80m/min, mentre la temperatura deve essere mantenuta tra 50°C e 160°C.
Le proprietà fisiche degli elettrodi possono essere regolate comprimendoli in un processo di calandratura. La calandratura richiede velocità precise dei rulli e il mantenimento di temperature di questi ultimi comprese tra 50°C e 250°C.
Segue una fase di taglio e stampaggio per portare gli elettrodi alle giuste dimensioni. Segue una fase di essiccazione sottovuoto per rimuovere l'acqua in eccesso e richiede una pressione di esercizio compresa tra 0,07 e 1000 mbar e una temperatura compresa tra 60 e 150°C. Dopo questa fase, gli elettrodi vanno nel locale asciugatura insieme ai separatori, già asciutti.
L'effettivo assemblaggio della cella comporta l'avvolgimento o l'impilamento degli elettrodi e del separatore in strati per formare una cella.
Nel procedimento finale, gli elettrodi e il separatore sono sigillati nel package, che viene poi riempita di elettrolita. Questo è un altro stadio che richiede alta precisione, con una pressione misurata a circa 0,01 mbar. L'invecchiamento della cella può comportare la misurazione di misurazioni della temperatura di 50 ° C per un periodo prolungato.
In ciascuno di questi processi, la misurazione accurata di più parametri, tra cui temperatura, pressione, tensione, planarità e spessore, è fondamentale per garantire la qualità richiesta.
Mantenere misurazioni precise durante tutto il processo di produzione della batteria è fondamentale per garantire la sicurezza e la qualità della batteria finita, oltre che per ridurre al minimo gli sprechi. In questo modo, i produttori possono evitare di rottamare parti e materiali e perdere tempo di produzione, assicurandosi di poter soddisfare la crescente domanda di batterie.
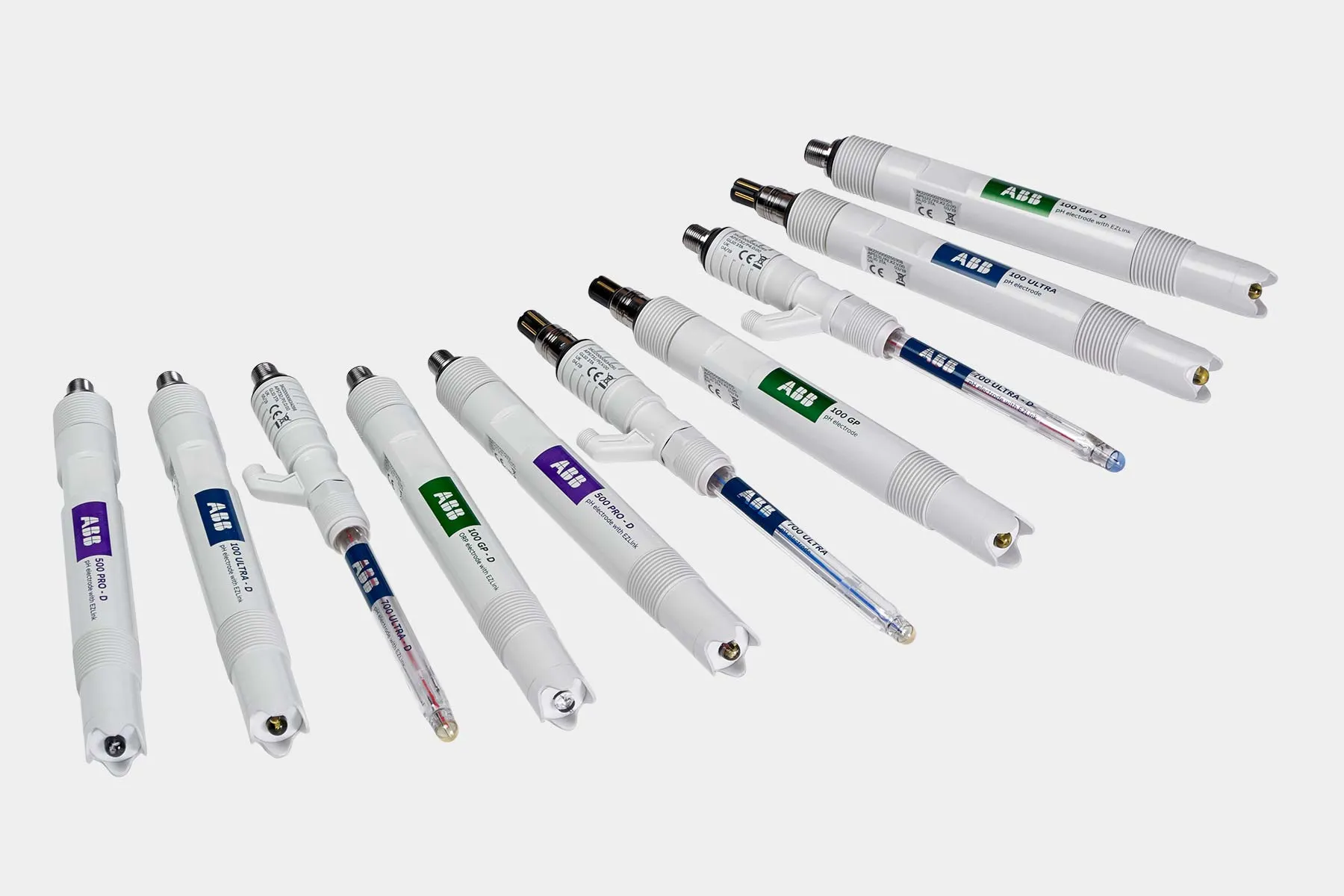
A prova di futuro grazie alla misurazione digitale
L'ultima generazione di dispositivi di misurazione digitali rappresenta uno strumento decisivo per il futuro dell'industria delle batterie. Con tecnologie all'avanguardia come microscopi elettronici a scansione e sistemi di imaging ad alta risoluzione, i produttori possono analizzare i materiali delle batterie a un livello di dettaglio senza precedenti, ottenendo informazioni precise sulle loro proprietà fisiche e chimiche. Ciò consente loro di esplorare nuovi processi e materiali e di portare avanti l'innovazione in questo campo. Inoltre, questi dispositivi di misurazione digitali consentono cicli di sviluppo del prodotto più rapidi, frequenza di guasti più bassa e costi complessivi ridotti migliorando il controllo della qualità durante tutto il ciclo di produzione. Inoltre, i dati raccolti da queste tecnologie possono essere utilizzati per sviluppare solidi modelli predittivi che identificano le aree in cui sono necessari miglioramenti per ottimizzare le prestazioni della batteria e prolungarne la durata.
In definitiva, l'integrazione di dispositivi di misurazione digitali nel settore delle batterie crea opportunità per soluzioni energetiche più pulite che svolgono un ruolo fondamentale nell'affrontare le sfide del cambiamento climatico, affrontate a livello globale.