—
motion service
La scienza dietro l’affidabilità degli impianti
Andrea Falcone
Motion Drives Service Manager di ABB
Evitare gli stop inattesi delle macchine è cruciale per le aziende: si evitano così elevati costi, mancati introiti e problemi con i clienti.
Ma come si raggiunge un simile risultato? Ce lo ha spiegato Andrea Falcone, Motion Drives Service Manager di ABB
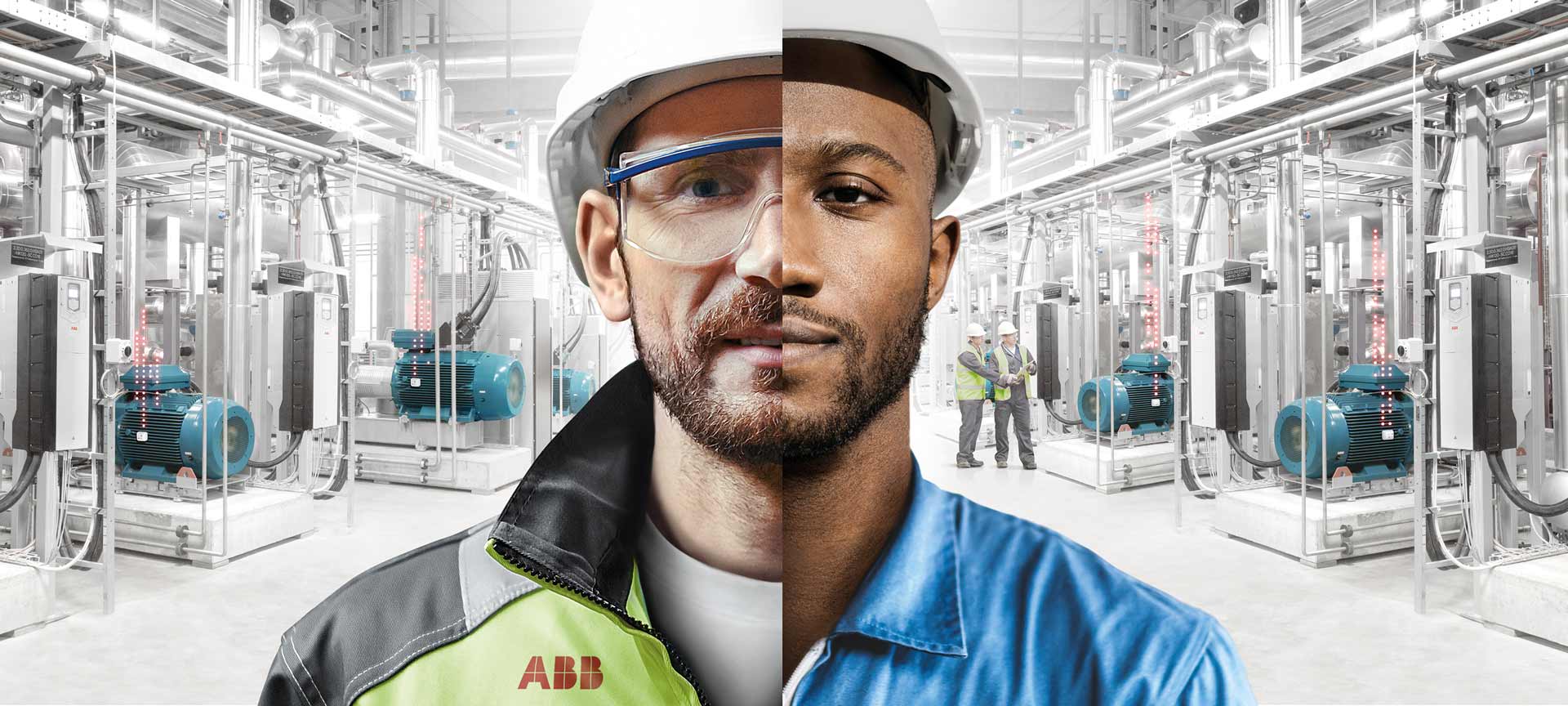
Come si misura la produttività di una macchina o di un impianto?
Sicuramente calcolando la quantità di prodotti che è in grado di realizzare in un determinato lasso di tempo.
Ma come quantificare la produttività quando il processo è fermo a causa di un guasto, un malfunzionamento o un altro problema di qualsiasi tipo?
Il conto è presto fatto: produttività zero. Per questo è fondamentale adottare le strategie più opportune al fine di ridurre al minimo gli stop inattesi.
Per sapere quali, abbiamo parlato con Andrea Falcone, Service Manager di ABB.
Andrea, qual è l’impatto di un fermo impianto non programmato per l’economia di una azienda?
Qualsiasi azienda ha dei KPI produttivi che identificano il loro livello di efficienza nei confronti di un mercato che sempre di più richiede risultati sfidanti e, di conseguenza, una elevata affidabilità.
L’analisi di questi parametri aiuta a comprendere dove intervenire per aumentare le proprie performance, essere vincenti e conquistare maggiori quote di mercato.
È facile comprendere come, all’interno di questo contesto, un fermo impianto non programmato (derivante ad esempio da un guasto o da un’altra criticità) incida negativamente in base alla sua durata e alla facoltà dell’azienda di sopperire alle forniture con scorte a magazzino.
Ogni processo industriale ha le proprie peculiarità, ma in generale posso dire che un impianto che si ferma per cause impreviste deve far fronte ai tempi necessari alla gestione degli scarti di lavorazione, all’individuazione del guasto, alla sua risoluzione e al tempo necessario per la ripartenza. Tutto ciò contribuisce a determinarne l’impatto economico, che somma non solo i costi diretti derivanti dalla risoluzione del problema (manodopera, parti di ricambio ecc.), ma anche dalla mancata produzione e dal rischio della perdita di clienti.
Sono proprio questi ultimi due fattori che incidono maggiormente e l’unico modo per ridurre i rischi è puntare sul mantenimento della piena affidabilità con il supporto di esperti del prodotto.
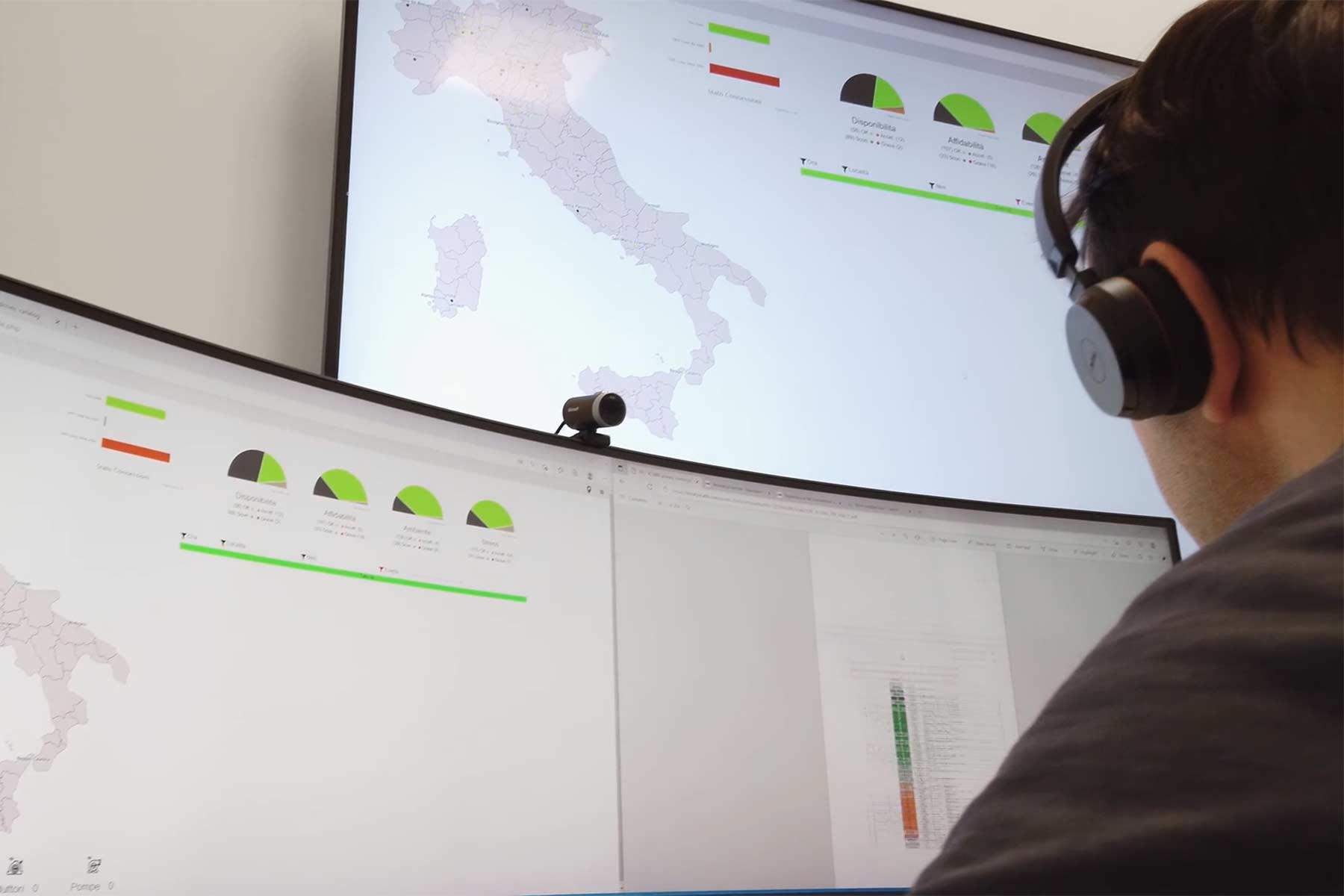
Ora che abbiamo compreso gli effetti, come facciamo a capire anche quali sono le cause di un fermo impianto non programmato e le possibili azioni da intraprendere per evitarlo?
La principale causa è la riduzione di affidabilità derivante dal tempo, dal ciclo di funzionamento e dall’ambiente in cui l’impianto lavora. Queste tre variabili influiscono sull’invecchiamento dei componenti, con un inevitabile aumento del rischio di guasto.
Per ridurlo è opportuno gestire l’impianto con attività manutentive periodiche adeguate e azioni correttive sull’ambiente.
Per fare un esempio, un investimento iniziale di pressurizzazione e filtraggio d’aria di una cabina elettrica e la sostituzione di quei componenti che hanno un degrado fisiologico nel tempo può contribuire all’incremento dell’affidabilità di un impianto complesso e alle sue performance.
—
L'affidabilità determina la capacità di un prodotto o sistema di funzionare e operare in specifiche condizioni e per un determinato periodo di tempo.
Come si misura l’affidabilità di un impianto industriale?
In generale l’affidabilità determina la capacità di un prodotto o sistema di funzionare e operare in specifiche condizioni e per un determinato periodo di tempo. Misurando questo parametro su un singolo prodotto o impianto industriale, osserviamo che le variabili che possono farlo variare rimangono principalmente sempre le stesse: il ciclo di funzionamento, il tempo e l’ambiente.
Ci sono parametri ben definiti che possono determinare l’affidabilità di un prodotto o di un impianto, come il Mean Time Between Failure (MTBF), ma questo presuppone che gli eventi imprevisti si siano già verificati. L’obiettivo principale deve rimanere quello di eliminare, per quanto possibile, le variabili prevedibili ed essere pronti a gestire le altre.
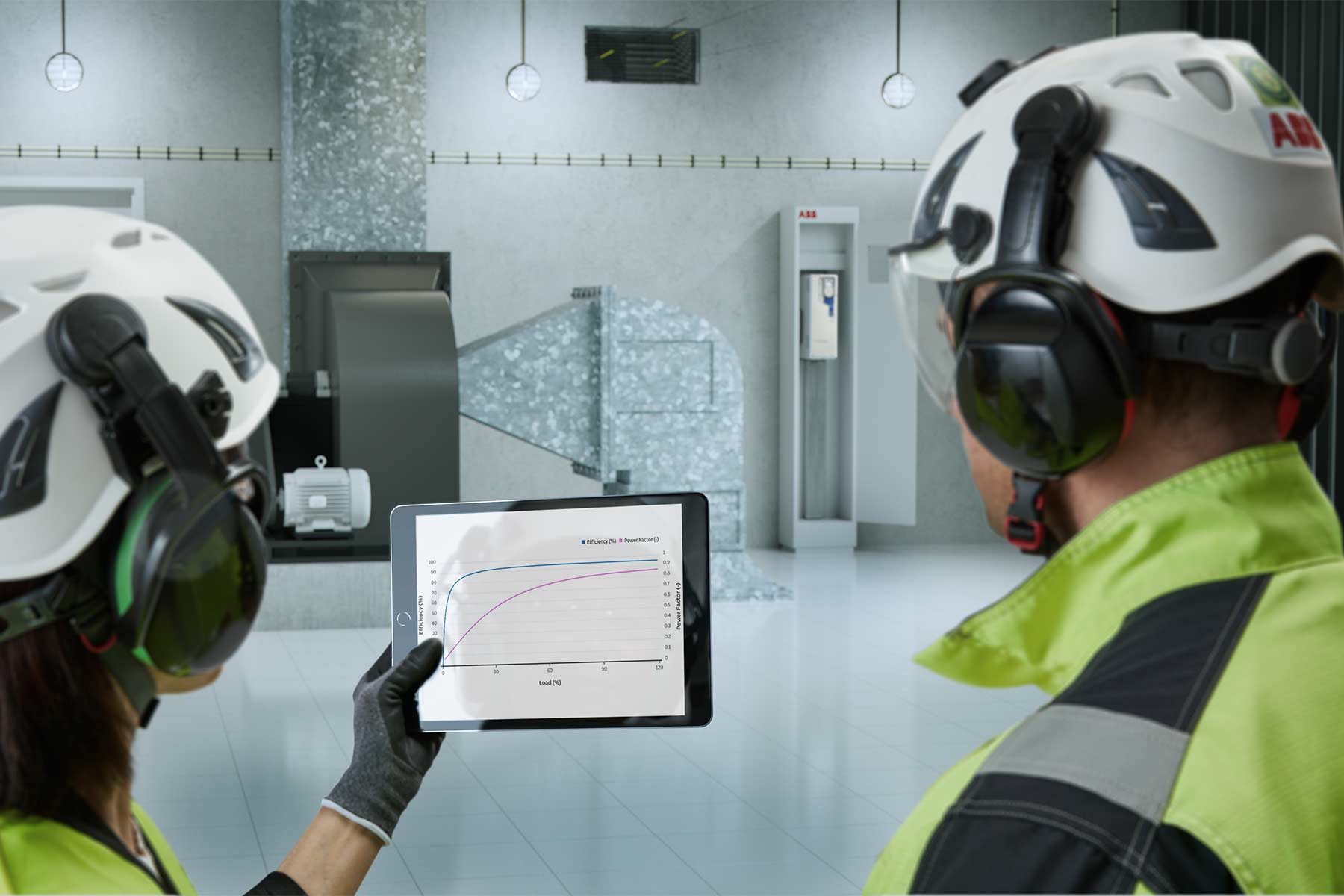
Quanto può rivelarsi complesso implementare strategie utili a ridurre gli stop inattesi?
Sicuramente non è semplice capire dove potrebbero esserci delle criticità, né come intervenire in modo efficace. Inoltre, una grande azienda ha al proprio interno prodotti di diversa natura e di diversi costruttori: questo rende praticamente impossibile formare un dipendente al fine di affrontare ogni genere di evenienza.
Oltre alla predisposizione del cliente, entra in gioco anche la responsabilità del fornitore nell’istruire gli operatori in modo che possano avere una visione delle criticità e stabilire delle priorità per una pianificazione adeguata dei budget manutentivi.
Dal canto nostro, in ABB ci impegniamo a mantenere la massima affidabilità dei nostri prodotti. Quando ci troviamo fronte a nuove installazioni eseguiamo dei Life Cycle Assessment per identificare le condizioni di partenza e, sulla base della nostra lunga esperienza con molteplici realtà industriali, stabilire le azioni da intraprendere per mantenerle inalterate nel tempo.
—
In ABB ci impegniamo a mantenere la massima affidabilità dei nostri prodotti
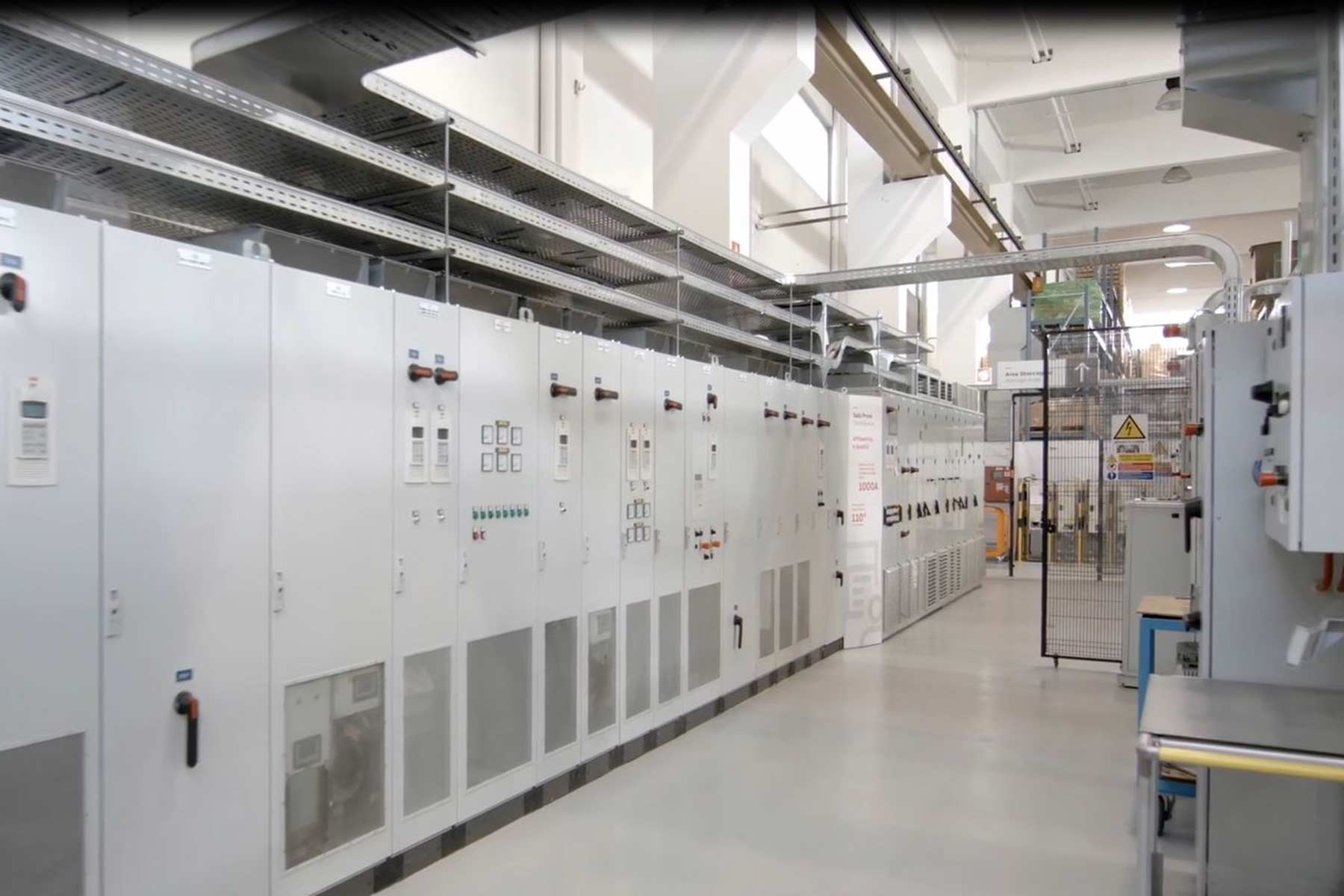
Al di là della (pur importante) questione economica, quali sono altri vantaggi nell’avere impianti affidabili e produttivi?
Un impianto affidabile permette a una azienda di concentrarsi su altri fattori, come analisi di mercato e l’opportunità di accettare nuove sfide.
Non dimentichiamo poi che un impianto perfettamente operativo elimina molte cause di frustrazione per gli operatori, con evidenti benefici a tutti i livelli aziendali.
In che modo un partner come ABB può supportare i propri clienti nel migliorare l’affidabilità di processi e impianti?
Grazie alla qualità dei prodotti ABB, alla formazione del personale tecnico e alla qualità dei servizi che eroga. Come Service Motion su Inverter e Motori siamo presenti in più di 70 paesi nel mondo per garantire servizi e supporto ai nostri clienti; inoltre, localmente possiamo contare su una organizzazione di oltre 170 persone motivate e capaci di sopperire a tutte le esigenze industriali più sfidanti.
L’obiettivo è assicurarci che chi si affida alle nostre soluzioni abbia la certezza di aver scelto un partner che possa aiutarlo a crescere e ad affrontare le sfide che il mercato pone quotidianamente. Il know how e l’esperienza che acquisiamo giornalmente, lavorando con aziende di ogni genere, dimensione e settore applicativo, arricchisce tutti, e ritengo che questo sia il modo migliore per aiutare i clienti nel proprio lavoro.
Offriamo un portafoglio Service che abbraccia tutte le necessità pratiche di cui abbiamo parlato: si parte dalla formazione certificata per i dipendenti, passando attraverso la manutenzione preventiva dei propri Asset, fino alle soluzioni digitali di remote monitoring dei dispositivi. Ciascuno di questi passi è parte integrante del percorso verso l’affidabilità.
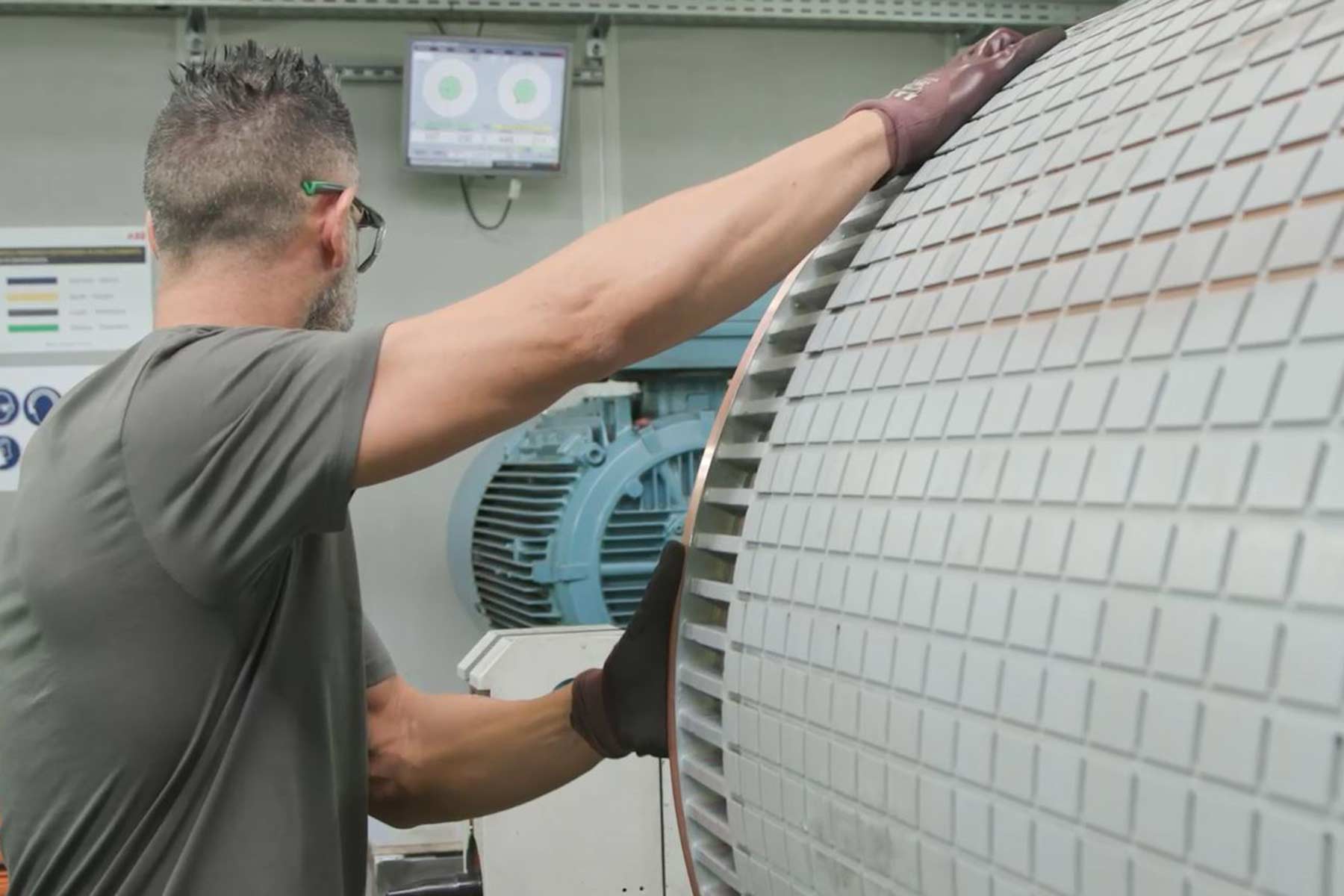
In un futuro ideale, quale potrebbe essere il punto di arrivo di queste soluzioni?
Sono convinto che il futuro ci riserverà molte soddisfazioni da questo punto di vista.
A mio parere la principale sarà relativa alla digitalizzazione: sicuramente servirà un cambio culturale da parte degli utilizzatori, ma l’analisi tramite algoritmi dei dati raccolti sul campo ci aiuterà tantissimo nel dare risposte rapide e a ridurre ulteriormente gli stop e le tempistiche di ripristino.
E non dimentichiamoci dell’approccio preventivo, calcolato sulla base di azioni manutentive dettate dal livello di stress misurato dei componenti.
Infine, i costi: avremo una visione immediata dell’incremento delle performance e dei risparmi ottenuti.
Si tratta insomma di una sfida stimolante, che in ABB abbiamo già accettato grazie a investimenti, professionalità e lungimiranza.