—
Affidabilità e sicurezza
Condition Monitoring, un approccio versatile per l’affidabilità dell’industria
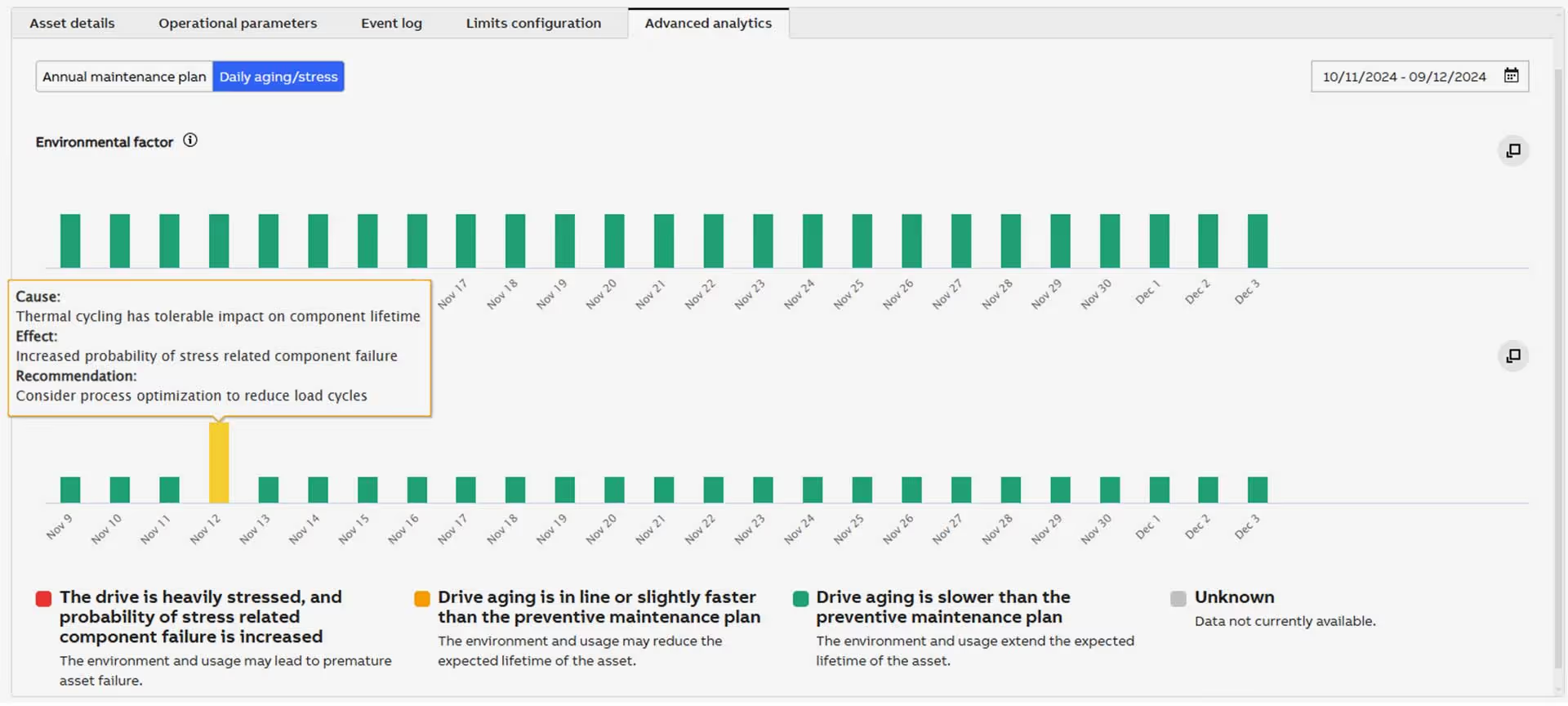
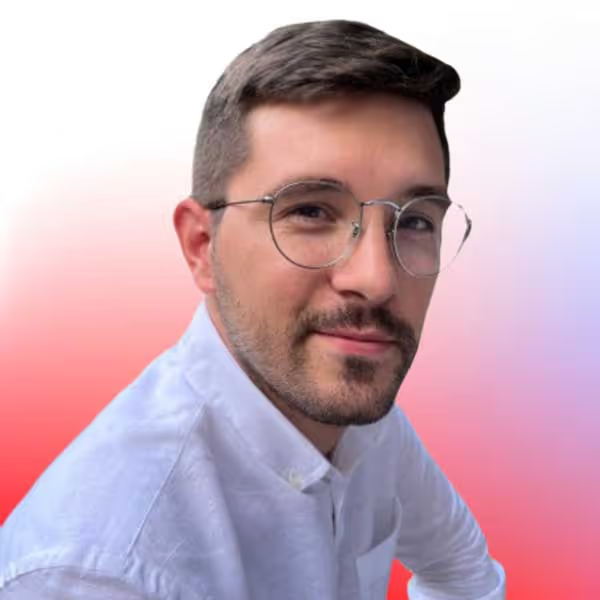
Andrea Bevilacqua
Digital Technical Specialist
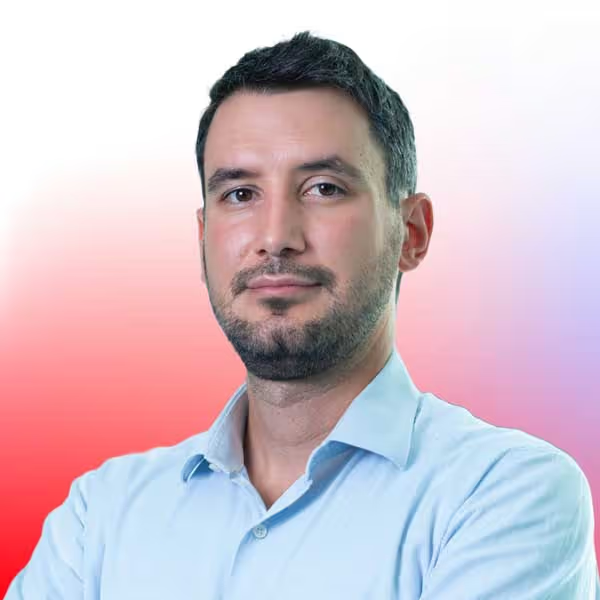
Stefano Colombo
Digital Product Specialist
Sommando le potenzialità offerte dalla sensorizzazione degli asset, e conseguente raccolta massiva di dati dal campo, e l’esperienza pluriennale di tecnici esperti, ABB è in grado di offrire un servizio di Digital Condition Monitoring di altissimo livello, utile per scongiurare stop inattesi degli impianti e gestire al meglio l’attività manutentiva.
Il Condition Monitoring è un’attività fondamentale per le moderne aziende: consente infatti di monitorare in tempo reale singoli dispositivi o interi impianti e di stabilire strategie di intervento basate sulle loro condizioni (da cui il concetto di Condition-Based Maintenance) o di agire nel caso si presentino delle anomalie.
Col tempo e con l’evoluzione tecnologica, all’esperienza di tecnici e professionisti si sono aggiunti anche la disponibilità di sensoristica connessa e la versatilità del cloud computing.
Le potenzialità di questo connubio sono molteplici, come ci hanno confermato Andrea Bevilacqua, Digital Technical Specialist, e Stefano Colombo, Digital Product Specialist.
In cosa consiste più in dettaglio il Condition Monitoring?
Innanzitutto, occorre precisare che non è una invenzione recente: è sempre esistito, solo che fino a non molti anni fa gli strumenti a disposizione erano ben diversi. Oggi, infatti, parliamo di Digital Condition Monitoring perché tutti gli strumenti utilizzati sfruttano la tecnologia basata su un approccio digitale: più intelligente, veloce, efficiente ed efficace.
È una attività che si prefigge lo scopo di valutare lo stato di salute degli asset e di monitorarli nel tempo, al fine di identificare possibili problemi prima che si verifichino o, in alternativa, di intervenire tempestivamente in caso di guasto.
L’obiettivo è quindi di prevenire possibili problemi o fermi macchina durante i processi produttivi.
Quindi è basato sulla raccolta dei dati? Come avviene materialmente il tutto?
Innanzitutto, in accordo con il cliente, si identificano gli asset critici da monitorare.
Se l’asset in questione è un motore elettrico, utilizziamo sensori chiamati Smart Sensor, che si occupano della raccolta e dell’invio dei dati. Possono lavorare con motori di qualsiasi costruttore, semplificando così l’applicazione su macchine di ogni tipo e provenienza per monitorarne i parametri vitali. Rispetto ad altre soluzioni sul mercato, sono estremamente semplici da installare perché non richiedono cablaggi né alimentazione. Per lo stesso motivo, non è necessario fermare l’impianto per collegarli: si applicano, si attivano e si connettono tramite Bluetooth Low Energy, cominciando a raccogliere dati fin da subito. Crediamo sia una soluzione straordinaria poiché, citando la nota regola di Pareto, fanno in proporzione l’80% del lavoro di strumenti ben più complessi con il 20% dello sforzo.
Se l’asset in oggetto è invece un inverter ABB, la connessione è altrettanto semplice attraverso due sistemi distinti: Connectivity Panel e Neta 21.
Connectivity Panel è dedicato ai nostri inverter di ultima generazione ACS880 e ACS580 e sostituisce il normale pannellino di controllo dato di serie: il nuovo pannello include un gateway certificato per la cybersecurity con una eSIM per l’invio verso il cloud delle informazioni e dei parametri rilevanti per il monitoraggio.
NETA-21 è il dispositivo Edge che permette di raccogliere i parametri dei drive connessi tramite una rete dedicata in fibra ottica, Panel Bus o Ethernet e inviarli al cloud tramite una connessione ad internet.
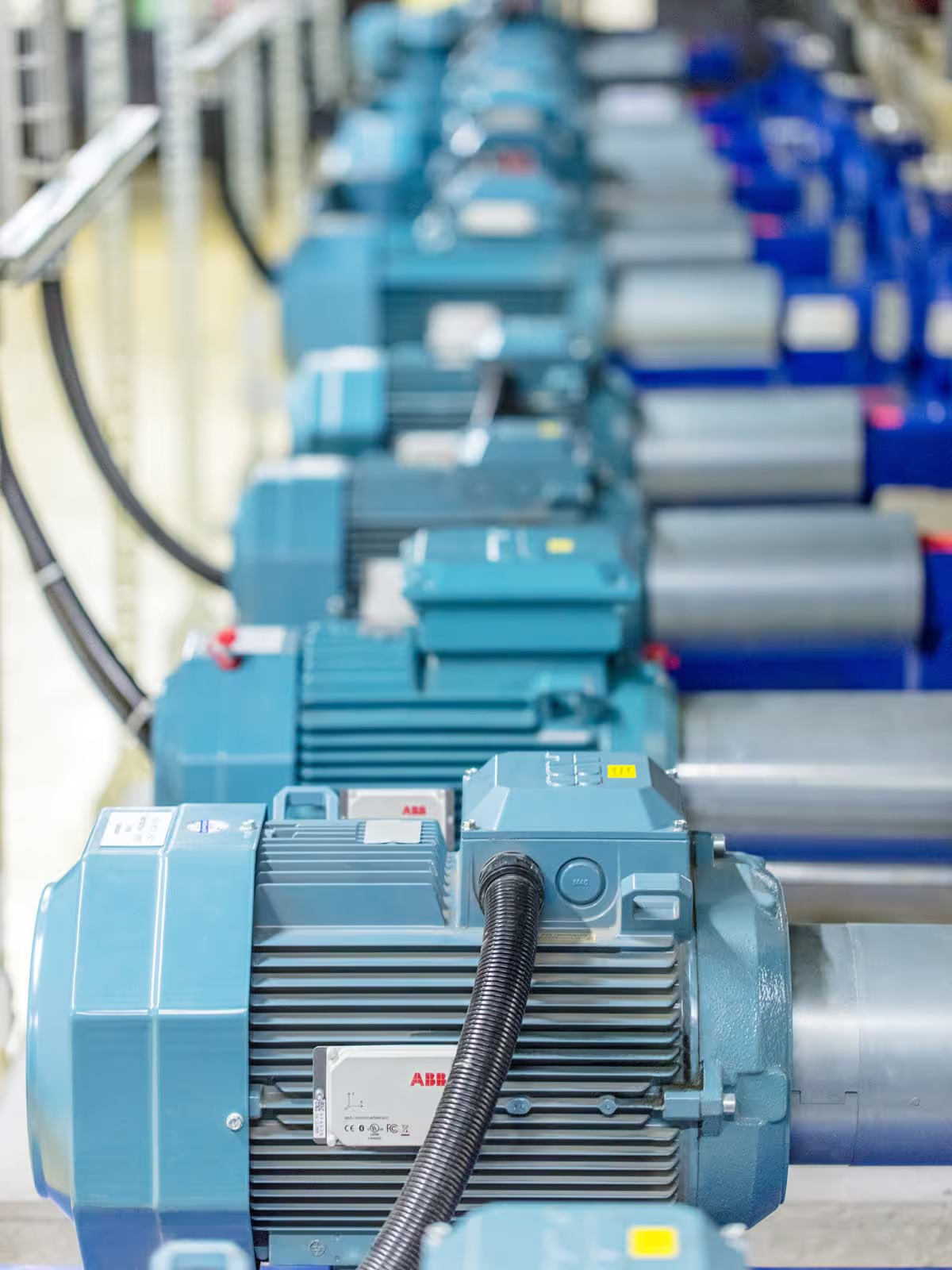
E in che modo questi dati contribuiscono a migliorare le condizioni e l’efficienza di un impianto industriale?
In moltissimi modi! Per prima cosa, grazie al monitoraggio costante si possono avere informazioni più precise. Un tempo, prima che il digitale rivoluzionasse questo settore, era necessario che un operatore rilevasse manualmente i parametri e li archiviasse opportunamente. Nella migliore delle ipotesi, si ottenevano un paio di rilevazioni al mese. Oggi possiamo contare su frequenze che, in base all’applicazione, partono da pochi secondi tra un rilevamento e il successivo e salgono a minuti, ore ecc.
Inoltre, non ci si limita a misurare temperatura e vibrazioni. Negli inverter rileviamo corrente, coppia, temperatura, consumo energetico e molto altro, mentre sui motori si tratta di vibrazioni, temperatura, condizione cuscinetti, velocità di rotazione e stima della potenza assorbita. Tutti questi dati vengono poi archiviati e analizzati in cloud, così da identificare le anomalie e intervenire per tempo.
La manutenzione dei motori tendenzialmente è schedulata in base alle ore di reale utilizzo; le informazioni ricavate dal campo ci permettono di stabilire se l’assistenza va anticipata (ad esempio se risultano temperature o vibrazioni anomale) o se può essere posticipata, dando magari la priorità ad altri interventi più urgenti.
Ci sono altri benefici per chi si affida al Condition Monitoring?
Oltre alla tempestività nel rilevare ed elaborare i dati, ci sono diversi altri vantaggi pratici.
Come accennato, non è necessario che una persona in loco si dedichi materialmente al rilevamento dei parametri.
In secondo luogo, il cloud offre alcune dashboard preconfigurate ma lascia ampio margine di personalizzazione in base alle necessità del cliente. Il cloud misura diversi KPI, come disponibilità, stato ambientale e surriscaldamento, stress e livello di invecchiamento delle macchine, ma possono essere elaborati anche report intermedi utili per focalizzare meglio l’analisi complessiva.
Infine, ad hardware e software si affianca la competenza del personale di ABB: l’utente non viene lasciato in balìa di numeri e grafici, ma viene seguito passo dopo passo affinché possa concentrarsi sul proprio core business. Oltre ad alert automatizzati, che ci informano di potenziali anomalie in corso, analizziamo ulteriormente i dati per rilevare ulteriori derive. La grande quantità di dati raccolti, infatti, si presta a essere interpretata in vari modi e in tempi diversi: come, ad esempio, per comparare periodi simili in anni diversi o per valutare altre variabili.
Tutto questo viene monitorato in delle sale dedicate nei nostri siti di Vittuone e Lucca da tecnici che informano l’utente solo quando necessario.
Mi rendo conto che, viste così, possano sembrare davvero tante caratteristiche da gestire, ma ABB ha lavorato per renderle di facile fruizione anche per utenti non esperti in materia.
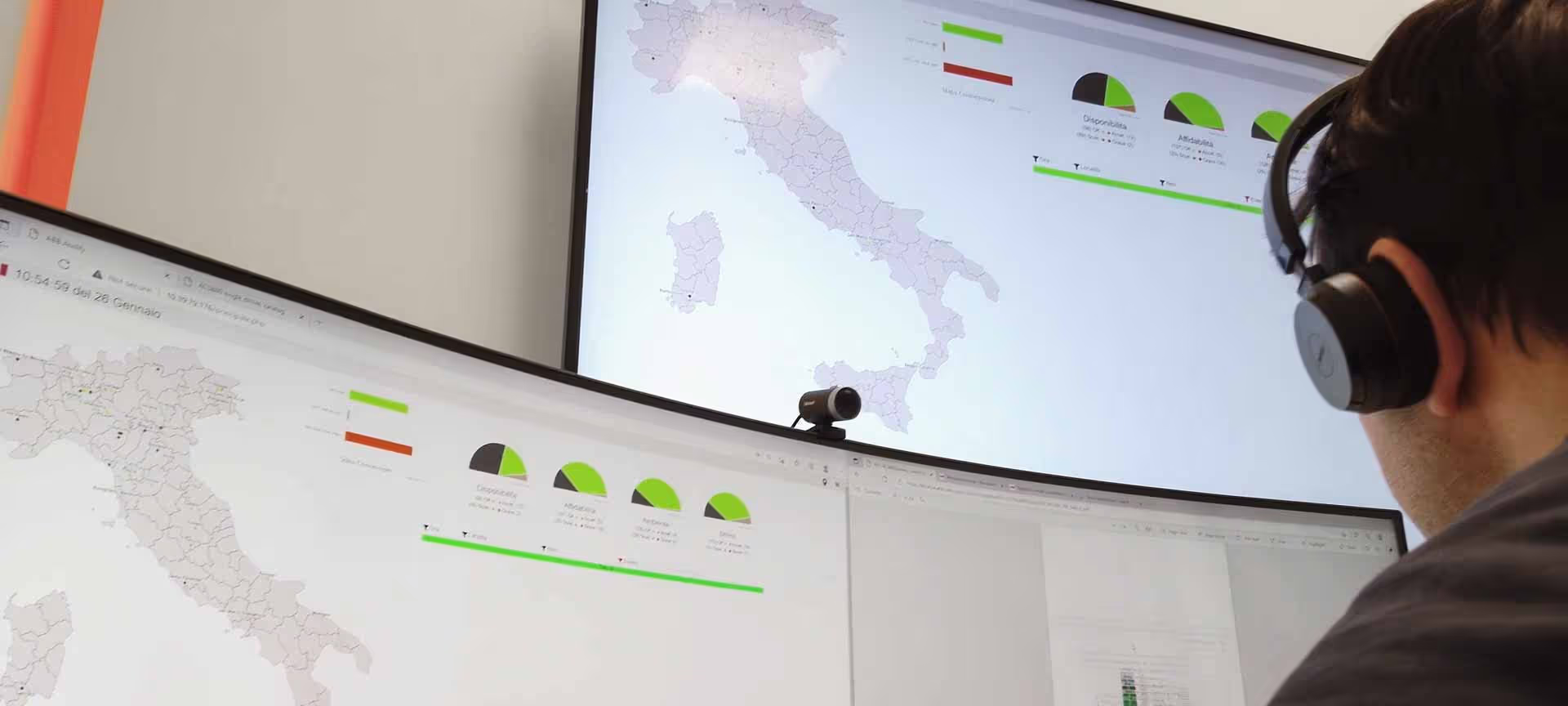
Un tema chiave è quello dell’efficienza energetica; il Condition Monitoring è utile anche in tal senso?
In maniera indiretta, sì. Non nasce per efficientare impianti e processi, ma svolgere la corretta manutenzione solo nel momento in cui è necessaria consente di avere macchine che funzionano meglio, non danno problemi e non rischiano stop inaspettati.
La raccolta dati permette inoltre di recuperare anche informazioni sui consumi. Avere tutto sotto controllo consente di identificare possibili problematiche o di intervenire per migliorare i processi rimodulando l’uso dei motori, le velocità, l’accensione o lo spegnimento ecc. Anche il semplice confronto tra l’assorbimento e la potenza nominale mostra un dato interessante legato all’efficienza effettiva, ma con i nostri sensori siamo in grado di spingerci ben oltre.
In che senso “spingersi oltre”?
I dati che raccogliamo sono una fonte incredibile di informazioni. Un inverter che si surriscalda può essere indice di un problema legato a quello specifico dispositivo, ma se il surriscaldamento colpisce più componenti all’interno di una cabina il problema può essere un altro.
È un caso reale che ci è capitato di affrontare e che ci ha permesso di segnalare al cliente un guasto all’impianto di climatizzazione di una specifica cabina elettrica.
Una valutazione analoga può essere fatta distinguendo tra stagioni diverse o tra installazioni simili in luoghi differenti. L’usura delle ventole del sistema di raffreddamento sarà diversa e, di conseguenza, anche la relativa manutenzione.
Come visto, un singolo problema può nasconderne altri e per ridurre al minimo l’insorgenza di potenziali problematiche sono fondamentali non solo la bontà degli algoritmi che analizzano continuamente i dati, ma anche la competenza di tecnici che eseguono ulteriori valutazioni basate sulla propria esperienza.
A Vittuone e a Lucca, uniamo questi due aspetti in due control room dove i nostri tecnici monitorano costantemente gli impianti dei clienti abilitati al servizio di monitoraggio delle condizioni. Attraverso schermi, vengono segnalati alert e criticità.
Per i clienti interessati ad approfondire, organizziamo visite e dimostrazioni mirate, entrando nel dettaglio del servizio.